Applications
Woodworking
CNI Group designs and produces a wide range of technological solutions aimed at the woodworking sector (from the carpenter/small craftsman to large industry). Already at the end of the 70s CNI includes the design of the first systems for multi-axis movement not yet present among PLCs.
Subsequently it develops the first CNC numerical control dedicated to drilling and milling work centers for panels.
These innovations allow specialization for most of the types of machines in the sector from the first processing (multi-blade machines, trimming machines, cutting machines), to solid wood (planers, moulders, multi-blade machines, tenoners, squaring machines, profiling machines, drilling machines, sanding machines, cutting machines, optimizing machines, painting machines, clamps, mortising machines, lathes, loaders/unloaders, multi-processing work centers, anthropomorphic and Cartesian robots for painting/finishing) to the panel (sectioning machines, edgebanders, squaring-edgebanders, cutters, drilling/inserting machines, pantographs, painting/finishing machines, folding machines, presses, loaders/unloaders, drilling-milling machines).
Panel Working
Panel processing has moved the big numbers in the wood sector in the last 40 years, the main use of panels is in furniture, which we all have in our homes. Given the great demand for pieces, the need arose to create machines for all the phases of panel processing and make them gradually more and more performing for the continuous evolution of the sector. The great variability of pieces, sizes and processes has immediately highlighted the need to create electronic systems and numerical controls dedicated to the sector, but also of software to assist in programming these systems, which were intuitive and easy to use from the operator’s side, also given the growing difficulty in managing batches of pieces different from each other. CNI Group sensitive to the needs born on the market, has developed specific software for the panel, such as cutting optimizers for sectioning machines, CAD/CAM for drilling-milling work centers, line supervisors, production statistics managers, scheduled maintenance as well as multiple HMI for dedicated equipment.
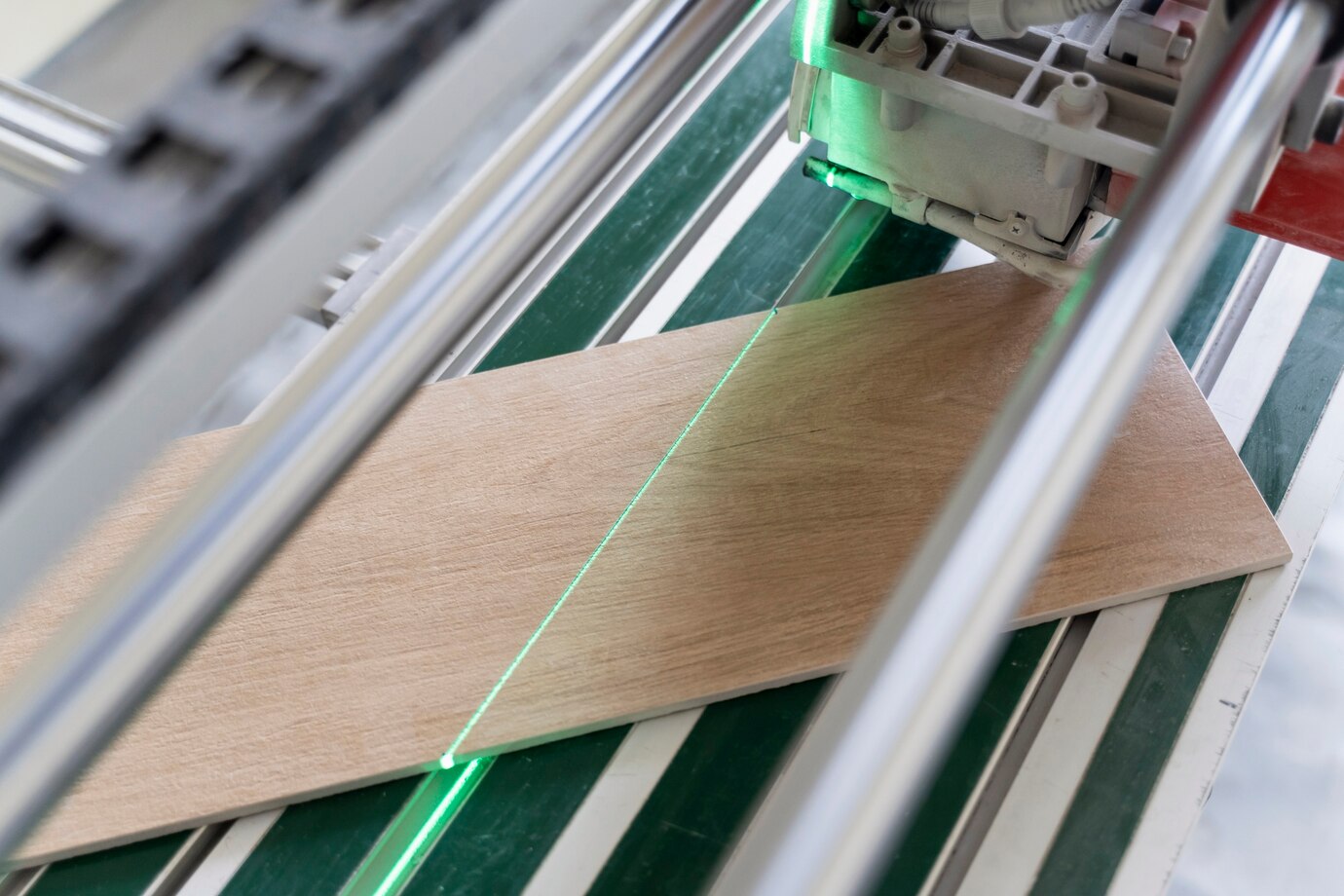
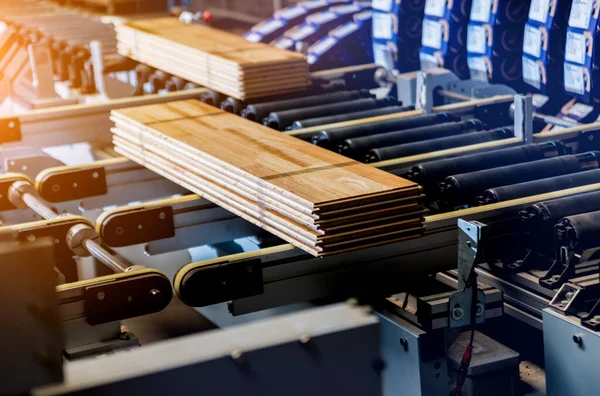
CNI has been automating high-productivity automatic lines for all phases of panel processing since the 1980s, normally consisting of: automatic loaders, sectioning machines, squaring-edging machines, drilling-milling machines and unloaders. For these lines, CNI has supplied both the numerical controls for the machines and the software for their programming and plant supervision. After over forty years of activity, CNI Group can boast thousands of system installations on panel processing machines, thanks also to long-lasting partnerships with internationally renowned customers (Biesse Group) in the production of technologies for the wood sector. To complete the automation needs for panel processing, given the great experience gained with vision systems in the Musa division, CNI Group wanted to create an automatic bench for dimensional verification of the processes performed on the panel: Wood Scan, supplied to the main manufacturers of pieces.
Wood window frame processing
CNI manages high-capacity production machines and lines for the wooden window and door sector. The composition of the line, the processes to be performed and the performance required are conceived, designed and created according to customer specifications, ensuring interfacing with existing management systems to integrate them perfectly into the customer’s production context. As for the panel, the complete management of a production line for window and door frames requires various skills that can be found in the Group’s Business Units: High-performance multi-center numerical controls to be able to move and interpolate hundreds of axes in groups along the entire path of the line, with customized logic and kinematics, but above all guaranteeing performance and execution times that cannot be found among the products of its competitors.
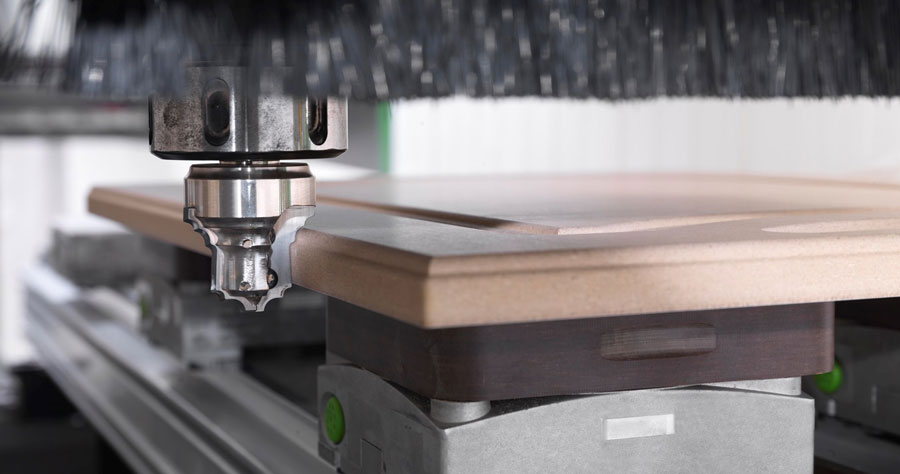
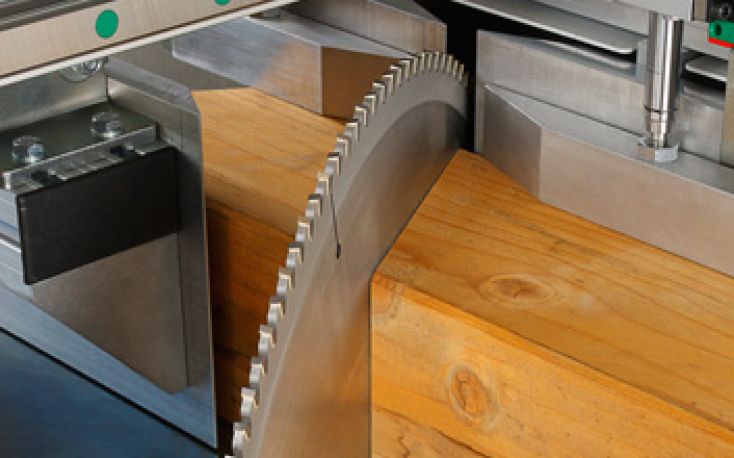
Supervisors capable of managing the entire flow of information on the line like an orchestra conductor: interfacing with the customer’s management system for the acquisition of the batches to be produced, sending the work programs to the machines, management of consents, management of automatic warehouses, collection of statistical production data and any special requests for adaptation from the customer. CAD/CAM systems integrated into the supervisor to automatically generate programs for each individual machine making up the line. The automatic generation of programs immediately before their execution, starting from the data passed from the customer’s management system, guarantees maximum flexibility of the system. Given the complexity of the lines, the processes and the pieces to be produced, manual programming by the operator would in fact be too difficult and at risk of error. Inspection and quality control systems for production integrated with line automation allow the identification of non-compliant products and their elimination from the production flow.